Fixturing for the Automated Age
Koma Precision’s booth at IMTS 2022 features practical demonstrations of rotary tables, right angle heads and more.
Share





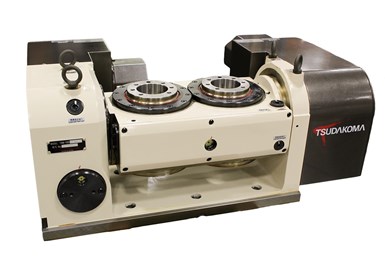
Koma Precision distributes Tsudakoma’s line of rotary tables. The pictured table is part of the TWM line, which best pairs with high-production single- or dual-spindle vertical machining centers that require five-axis machining.
Live demonstrations with customer parts headline the show at Koma Precision’s bright green booth. This IMTS, the company is showcasing rotary tables in common fixturing setups for automotive parts. In addition to stock Tsudakoma rotary tables, Koma Precision is also emphasizing its specialty rotary tables, which are born from collaboration between Tsudakoma, Koma Precision and the end user.
Koma Precision is also showcasing NEO right angle heads, which the company says add versatile high-torque and coolant-through options to its line of machine tool accessories. Video displays highlight overhead hydraulic products for high-production horizontal and vertical machining centers, as well as the company’s machine tool presetters with auto-measuring functions.
“Automation is the trend of the industry,” says company president David Meo, and all the products Koma Precision is demonstrating at the show are primarily optimized for robotic tending rather than manual tending.
Visitors can stop by the Koma Precision booth to pick up a free pen and notepad.
Related Content
-
Chuck Jaws Achieve 77% Weight Reduction Through 3D Printing
Alpha Precision Group (APG) has developed an innovative workholding design for faster spindle speeds through sinter-based additive manufacturing.
-
Medical Shop Performs Lights-Out Production in Five-Axes
Moving to five-axis machining enabled this shop to dramatically reduce setup time and increase lights-out capacity, but success relied on the right combination of workholding and automation.
-
How to Mitigate Chatter to Boost Machining Rates
There are usually better solutions to chatter than just reducing the feed rate. Through vibration analysis, the chatter problem can be solved, enabling much higher metal removal rates, better quality and longer tool life.